BUILT TO BLAST - HOW TO MAKE ROBOTS LAST FOR DECADES
BUILT TO BLAST - HOW TO MAKE ROBOTS LAST FOR DECADES
Abrasive blasting sets up a uniquely challenging environment for machines and technology.
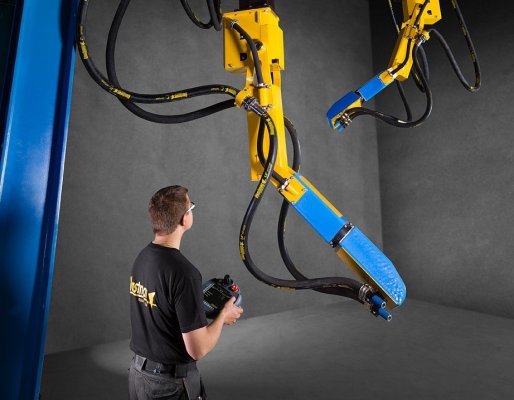
Blast cleaning with robots is a highly effective process with large nozzles, high pressures, and hard abrasives. During blasting, high-velocity particles are constantly rebounding creating erosion and dust in the surroundings, much more with robotic blasting than with traditional manual blasting. The more advanced the technology in the blast room is, the more know-how is needed to keep it functioning. This environment was the starting point for the development of our robots 40 years ago. How to make robots last for decades? That is the key question for us.
The roots of Blastman robots lay in the early 1980s in a Finnish heavy industry company called Tampella.
The company had lots of experience in making durable machines in harsh conditions, such as the mining industry. Engineers of Tampella knew the key guideline for makings machines that lasts for decades: simplicity. Based on this engineering excellence, experience, and guideline, the first generation of robots was born.
Blastman history and Tampella
Robotics has come a long way since the early 80s and the first generation of robots. Blastman has always put significant effort into systematic R&D - a lifeblood for a company like ours. In 2021, the fourth generation of Blastman robots was introduced. Guidelines for the design of 4th generation robots have been reliability, operability, simplicity, and ease of use. Technology has been upgraded to include the latest and most advanced components on the market. Still, the core value of making equipment to last decades has been upheld and no compromise was made on the durability of the robot.
The closer we are to the nozzle and abrasive jet, the more we need to protect our equipment.
In a blasting robot, the robot arm holding the nozzles is suffering the most from the abrasive rebound. In earlier robot generations, the robot arm enclosures were protected with polyurethane, which was durable and could absorb energy well, but it also added complexity and weight to the arm. As a result of our constant R&D, the 4 generation enclosures are now made from ultra-wear-resistant steel. Although steel is more expensive and more difficult to manufacture, it makes the structure lighter and simple - thus easier to maintain. This allows for a long lifetime of the equipment, fewer maintenance costs, and an increase in reliability.
Also, when it comes to dust prevention, IP ratings are again not enough for a blast room environment. For example, electrical cabinets located inside the blast room are heavily protected against the rebound and over-pressurized with compressed air to keep the dust away. Also, the telescope arm is pressurized. In addition, all bearings in the robot are sealed for life and we are using our 40-year experience also in selecting the correct bearing type, which can survive the environment.
Control room for two B20S blasting robots
While still having some cabinets inside the blast room, our aim is that all cabinets possible should be left outside the blast room. Proof of that is our newest generation 4 robot type B16XS which has electrical panels outside the blast room. This design allows for most of the delicate electrical equipment to be outside of the dusty blast cleaning environment. Also, running diagnostics for the robot is simpler since the electrical panels are located in a more ergonomic space.
In the electrical design, Blastman has incorporated OCT (one cable technology) for 4th generation robots. This allows for easier cable management and faster maintenance actions. The number of cables is minimized and all cables possible are internally routed to be protected from rebound and dust.
Naturally, all robots require maintenance. This is a fact and must be taken into account for the design of any machine. If some robot parts need extra protection or if a part is designed to be replaced at certain intervals, extra attention is paid to how to replace the protective element and do maintenance. Blastman robots come with a preventive maintenance schedule which is based on our 40-year experience of potential wear points and how to maintain protection there.
For Blastman, built-to-blast stands for more than technical details.
To have equipment up and running for decades we need to also focus on the layout design, adequate capacity calculations, and training of personnel. When these measures are done correctly right from the start, it greatly prolongs the lifetime of the robots.
All Blastman robot cells are designed and tailored to blast clean the workpieces with high efficiency and precision. Typically, the robot cell consists of a blast room, abrasive handling, ventilation, and other supporting functions such as a workpiece transportation system. In our design, we also consider the wear of the infrastructure around the robot, such as blast room walls, lamps, floor grids, and other machines supporting the operation. Abrasive handling, especially abrasive dust removal systems, should be properly designed to avoid excessive dust in the abrasive mix, which wears out hoses and blast pot components. In the fight against dust, the ventilation system should have enough power, the right filter material and properly working airflow.
Blastman Studio software
An important part of built to blast philosophy is training.
During programming, training operators are trained to program the robot so that the required blasting capacity and coverage are reached. A big portion of studies is also devoted to learning the right blasting angles, speed, and distances for minimizing robot wear. Maintenance training is focused on preventive maintenance, which derives from our experience – we know what the critical places are, we know how to protect them, and we teach the user to do preventive measures.
One could think, that bringing a highly sophisticated robot to the blast room is not a good idea, but this has been our bread and butter for decades.
Blastman robots are Built to Blast.
Timo Broström
Solution Engineer
Blastman Robotics Ltd
You might be interested in these articles
Company News Events
03. Mar 2025
Welcome to visit us at MECSPE, Bologna from March 5th to 7th.
Blog Posts Company News Events
16. Dec 2024
Season´s Greetings from Blastman Robotics Ltd
Company News Events
23. Aug 2024
BLASTMAN AT INNOTRANS 2024
Blog Posts Company News Events
22. Aug 2024
ABRASIVE BLASTING INVALUABLE FOR RAIL INDUSTRY
Company News Events
20. Jun 2024
BLAST CLEANING LARGE STEEL STRUCTURES FOR ENERGY INDUSTRY
Company News Events
20. Feb 2024
WE´RE EXHIBITING AT PAINTEXPO 2024
Blog Posts Company News Events
18. Dec 2023