Blasting Automation and Robotics Equal Best Efficieny
BLASTING AUTOMATION AND ROBOTICS ENABLE THE BEST BLAST CLEANING EFFICIENCY
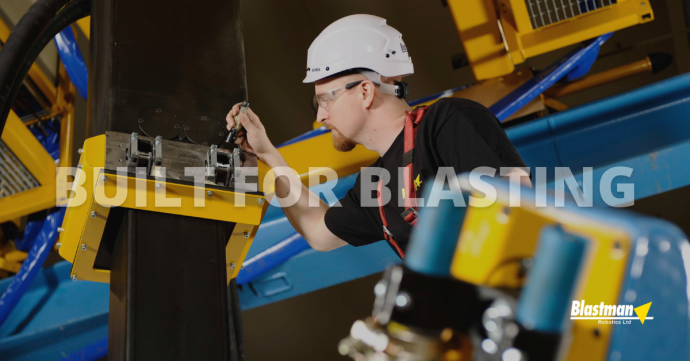
The original ways robots have proven their efficiency over other blast cleaning methods haven’t changed a lot over the decades. On the other hand, this just goes to show they stand the test of time. Larger nozzles and bigger hoses enable larger jet streams and bigger amounts of blast material. This principle doesn’t change. However, the benefits of blasting automation and robotics don’t end there.
There has been and is continuous development within blast cleaning robotics. The level of programming and maintenance proficiency has advanced, which in turn improved the equipment's already impressive reliability and lifetime. Simply put, the overall efficiency of the process has improved.
In this article, we look deeper into the different aspects that make the efficiency of blasting automation and robotics unrivaled.
Man + machine
To this day, there exists a certain mysticism about robots, and it is common to compare their abilities to those of humans. When industrial robots are in question, the comparison is typically induced with a slight fear of people gradually being replaced.
But if we are truly fair, throughout our existence, we humans have invented and refined tools to reduce the need for manual labor. When it all comes down to it, even sophisticated robots are only tools, and sometimes handing over a specific job to them is not only smart but borderline necessary. In this sense, a blasting robot is a friend, not a foe.
Manual blast cleaners must endure extremely harsh and exhausting conditions, while robots can operate tirelessly without breaks. Additionally, a robot needs a relatively small space compared to a manual worker. In fact, it is operable in such a narrow gap it wouldn’t even be ergonomically sensible for a human. If the object necessitates blast cleaning from high up, the robots can be fitted with telescopes that make the erecting of scaffolding or ladders unnecessary. The automated robotic blasting process is always prepared in a way that enables cleaning throughout the workpiece.
Utilizing blasting automation and robotics tremendously improves occupational safety but affects the human resources aspect otherwise as well. Manual blast workers stay in their profession for a maximum of two years before seeking other jobs. Meanwhile, those who have been given the opportunity to shift to operating robotic blasting have continued for 10 to 20 years. Shifting to automation reduces long sick leaves and the need for training new workforce as more long-lasting professionals stay in the picture. Difficulty in finding a young workforce for manual blasting is, in fact, a global trend, and it’s no wonder since there is an abundance of more pleasant work. One of them being none other than abrasive blasting with robotics.
Blasting automation and robotics contain many benefits over manual blasting.
Read more about the different factors that make switching to or upgrading automated robotic blasting a smart move.
In blasting automation and robotics, optimization is efficiency
From a human perspective, productivity is the second most important reason to replace manual blasting with automation. When industrial processes are scrutinized, it all inevitably comes down to numbers.
While human laborers can only operate one blasting nozzle at a time, robots can be fitted with two each. Additionally, robots have no trouble handling 19-millimeter nozzles at a pressure of 10 bar, while the respective specifications need to be limited to 8 mm and 5 to 6 bars for humans. This difference in pressure affects the abrasive velocity, which in turn affects process efficiency. With high 10 bar pressures, the robot accelerates the abrasive to 200 m/s, whereas manual blasters or other blast cleaning methods fall far short of this.
While with blasting automation and robotics, it is possible to blast clean 200 square meters per hour, the typical efficiency of a manual blast operator is 10 m² per hour. Of course, it is possible to manually blast more than that, but the higher the pace gets, the more it begs the question of whether the cleaning quality is sufficient. With a robot, there is no question, as it always does what it’s programmed to do.
The higher the pressure, the more powerful the blast can obviously be. However, the maximum pressure is not always necessary, not to mention optimal. In fact, robots' efficiency can also be perceived through their ability to operate accurately and consistently with lower pressure. For example, for an aluminum train car, 10 bars are too much. Yet the robots handle the same car, which takes four people a day to process, in 20 to 25 minutes.
Optimization also takes into account the number of operators and their ability to perform. Manual laborers often need to pause their work to switch positions and tug and pull the blasting hoses as they go. The more workers have to move the less efficient they are. Meanwhile, robots move in fluid and continuous movements and have brackets to move the hoses with them. A reasonable number of workers inside the one blasting chamber is usually 2 to 4 people.
Some workpieces are repair jobs coated with old paint. This causes more work phases, and the more phases there are with a certain piece, the more time robots win per square meter.
Robotics vs. wheel blasting
The efficiency of robotics can be underlined not only by comparing it to manual blast cleaning but also to another automatic solution called wheel blasting. This method is based on a high-velocity spin wheel that propels abrasives to a certain direction. It is usually categorized as airless blasting since it doesn’t use a propellant such as compressed air.
To be completely cleaned, sloping and curved shapes and different notches and indents – spots that form shadows – must be blasted from many different angles. Even though a spin wheel can propel a huge amount of abrasive material, its blast doesn’t reach around corners. If the geometry of the workable object is complicated, a large amount of abrasive, accelerated to high speeds, simply misses its mark and hits the walls of the blast booth. A normal Blastman Robotics Blast robot has 8 axles, which enable nozzles to be positioned extremely precisely to desired spots.
There are also limitations to materials as blasting wheels can only use buckshot-type abrasives. In air-propelled blasting it is possible to use any kind of grain, enabling also the use of extremely hard and gritty materials that would break a blasting wheel through mechanical wear.
Robots are relatively maintenance-free in comparison to wheel blast machines. With robots, the most common maintenance procedure is hose replacement, which takes approximately 5 minutes. This means that not only is a robot practically always operable, but it’s also back in action astoundingly fast.
Blasting automation and robotics are easy to program
Automated robotic abrasive blasting follows a program that not only ensures that the robots know what to do but enables many advantages. Once the blast cleaning program is compiled, workpieces can be processed with it for years. The program is prepared on a computer in a 3D environment so that it doesn’t consume production time. This way, as the object arrives for its surface treatment, everything is ready.
Programming includes a simulation feature that demonstrates how the spray will hit surfaces and gives a cycle time for the blasting process. This makes it easy to optimize all the necessary specifications and plan a desired number of processed workpieces in a certain time beforehand.
In manual blasting, the abrasive is loaded in a hopper or a pot that is blasted empty and then needs to be refilled. A Blastman blasting robot, on the other hand, uses a blast pot with an automatic abrasive refill. This way, a program can run continuously for, for example, 20 hours until it’s finished, and the blast pot never runs out of abrasives. With large workpieces and long processes, continuity can significantly save time.
As a cherry on top, with Blastman’s robotics, it is possible to decide whether the system propels abrasive or only air, even determining this beforehand in the programming phase. By shutting down the stream of abrasive, it’s possible to clean the object from residual abrasive and dust.
Programming with Blastman Studio software
Myths surrounding blasting automation and robotics debunked
What surprises many is that the robotics used in Blastman’s solutions are its own. Blastman hasn’t utilized any common industrial robots but has instead designed its robotics specifically for abrasive blasting. Although it’s an easy assumption that such finely tuned equipment would be prone to give in, they are, in fact, bafflingly durable.
The robot’s arm closest to the blast’s rebound lasts for over 10 years. To be fair, from the maintenance point of view, it is more useful to compare the lifetime of blasting equipment through operating hours, which in robotics is in the thousands. Still, it says something that there are Blastman’s robots out there that have been in steady use for 25 years.
Sometimes, potential customers are under the impression that robotic solutions wouldn’t suit their long processes. As determined earlier, the bigger or more complicated the object, the smarter it is to utilize blasting automation and robotics. Because of the numerous plus sides of the method, the longer a blasting process lasts, the more benefits it reaps.
Every once in a while, the suitability of robots for processes where workpieces vary poses a concern. There is no need, since offline programming and its easiness enable flexible processing of small series as well.
It is also a natural assumption that operating a sophisticated blasting automation and robotics would require comprehensive know-how. In reality, Blastman has designed everything to be used without an engineering degree. It has even been stated that Blastman’s interface can be operated if one can use a PlayStation. Accessibility and user-friendliness are in natural demand as people operating the equipment are getting used to it with their everyday appliances, too. This is something that Blastman has taken into account and consciously improved.
Read more on how Blastman makes choosing blasting automation and robotics surprisingly easy.
The even more efficient future of blast cleaning
The first delivery of Blastman’s own programming software took place in the fall of 2021. Until that point, the company operated with a third party. Tailoring software for its own robots has made their operation even smoother and more user-friendly.
As mentioned in the beginning, the main principle of robotic blasting has stayed the same but this doesn’t prevent the process from being developed further. In the quest of making blasting automation and robotics even more efficient, one answer is reducing working hours with automatic programming and machine vision.
Robots don’t yet know where the workable object is and thus have to rely on the program. Machine vision can be used to identify certain points of the object, determine its accurate position, and, if necessary, shift the program to the correct position. This is especially useful if the placement of the workpiece has to be measured by millimeters or if it is too large to be moved around during the process.
Of course, the placement could still be determined manually with a laser, but as is the case with so many other things, automation could handle the same thing instantly, as well as reduce the risk of useless blasting and the need to renew work. Added accuracy equals added quality.
Blasting automation and robotics in the form of the two B16XS robots Generation 4.0
While blasting robots are highly efficient and durable, even they need maintenance. Proactivity—for example, automatic detection of an incipient hose breakage—can improve efficiency by providing the opportunity to schedule maintenance in advance for a time when production doesn’t happen to be running. This way, it won’t interrupt a process.
Other areas to which automation could be extended are, for example, the intake and expulsion of the workpiece and the monitoring of the abrasive mix. As the blasting material hits the processed surface it disintegrates and turns into dust. One way to improve the efficiency of the process is to monitor the dissolving material and determine whether the process is run with an optimal abrasive mix.
Automation in the overall monitoring of the space and process can provide valuable data that can benefit the utilization rate and lifetime of all the equipment needed in blast cleaning.
Read more about how Blastman sees the future of blasting automation and robotics.
You might be interested in these articles
Blog Posts Company News Events
15. Aug 2025
ABRASIVE BLASTING INVALUABLE FOR RAIL INDUSTRY
Company News Events
03. Mar 2025
Welcome to visit us at MECSPE, Bologna from March 5th to 7th.
Blog Posts Company News Events
16. Dec 2024
Season´s Greetings from Blastman Robotics Ltd
Company News Events
23. Aug 2024
BLASTMAN AT INNOTRANS 2024
Company News Events
20. Jun 2024
BLAST CLEANING LARGE STEEL STRUCTURES FOR ENERGY INDUSTRY
Company News Events
20. Feb 2024
WE´RE EXHIBITING AT PAINTEXPO 2024
Blog Posts Company News Events
18. Dec 2023