BLAST CLEANING METALWORKING MACHINERY
BLAST CLEANING METALWORKING MACHINERY
Case: AMADA AUTOMATION EUROPE LTD. Bennäs, Pedersöre, Finland
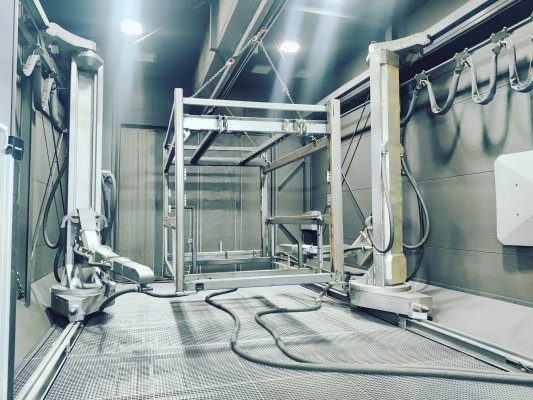
BACKGROUND
AMADA Automation Europe (AAE) is part of the global AMADA Group, in Japan. AMADA is one of the world’s leading manufacturers of high-technology metalworking machinery.
Amada made the decision to renew its surface treatment line, including blasting, painting, and drying chambers. All technological process is automatized, blasting and painting are done by robots.
Metalworking machinery
OBJECTIVES
The target was to replace the manual blasting process with robotics and to increase the efficiency and quality of blasting. The use and programming must be simple and easy as workpieces have a lot of variation.
Today blast cleaning is done with 2 robots, which are programmed using Blastman Studio. The entire room is integrated into the overhead conveyor system for maximum efficiency and reduced labor.
Blasting chamber for two Blastman robots and control stations
SOLUTION
Blastman solution is a fully automated pass-through blasting chamber. Workpieces are moving with overhead conveyors, which are integrated and communicating with the robots and blast room.
The core of Blastman supply are two wall-type robots B16XS and blast pot BP1100 which allow continuous operation of robots. The robots are supported by the complete blast room delivery by Blastman, including room enclosure, abrasive handling, and ventilation.
The robots work in automatic mode according to previously created blasting programs. Creation of blasting programs for the robot is done by operators using Blastman Studio software, developed by Blastman, especially for robots and the blasting process. It is intuitive software, creating and modifying of blasting programs is fast and easy.
TECHNICAL INFORMATION
Nozzel diameter | 16mm |
Number of nozzles/robot | 1 |
Blasting pressure | 8 bar |
Abrasive | Steel grit |
Degrees of freedom | 7 per robot |
Blasting rate | 130m2/h |
Programming | Offline: Blastman Studio |
Operation mode | Automatic |
RESULTS
The new blasting chamber works reliably as an important part of the surface treatment line. Blastman robots allow to achievement high-quality of blasting of surfaces. Customer production has greatly increased thanks to the high efficiency of the robots. Additionally, Blastman solution has greatly improved working conditions and workplace safety.
Blastman B16XS robots
Complete blast room delivery
You might be interested in these articles
Company News Events
03. Mar 2025
Welcome to visit us at MECSPE, Bologna from March 5th to 7th.
Blog Posts Company News Events
16. Dec 2024
Season´s Greetings from Blastman Robotics Ltd
Company News Events
23. Aug 2024
BLASTMAN AT INNOTRANS 2024
Blog Posts Company News Events
22. Aug 2024
ABRASIVE BLASTING INVALUABLE FOR RAIL INDUSTRY
Company News Events
20. Jun 2024
BLAST CLEANING LARGE STEEL STRUCTURES FOR ENERGY INDUSTRY
Company News Events
20. Feb 2024
WE´RE EXHIBITING AT PAINTEXPO 2024
Blog Posts Company News Events
18. Dec 2023