BLAST CLEANING OF LARGE CASTINGS
BLAST CLEANING OF LARGE CASTINGS
Case: Eisengiesserei Torgelow GmbH Torgelow, Germany
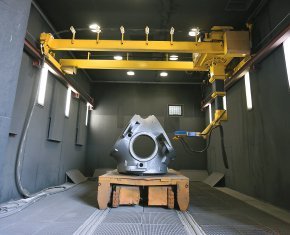
BACKGROUND
Eisengiesserei Torgelow GmbH is one of the biggest hand-molding gray cast iron and ductile iron foundries in Europe. With modern casting and production technology, the company can effectively produce heavy and complex castings. Having heard about Blastman technology the company also decided to upgrade its manual blasting to state of art robot blasting.
OBJECTIVES
The target was to robotize their manual blast room since blasting large castings manually is ineffective. There was a need to use a robot by programs and additionally manually by joysticks for touch-up blasting. Touch-up blasting is needed since possible casting failures are hidden and can be found after a robot blasting process. The old transport wagon was planned to be retained.
The EGT is one of the largest European hand
molding foundries with a capacity of 8,000 t /
month. It supplies finished components made of
gray and ductile iron with a blank weight up to
115 t and provides other services such as
modeling, simulation creation, and engineering.
Advantages of Automated Blast Cleaning
- considerable savings in production costs
- increased production capacity
- remarkable health and safety implications
- freedom to use any abrasive material
- desired surface cleanliness and roughness
- slight surface shaping by controlling the blast pressure
- working lifts and platforms are not needed
- increased fatigue strength of specific welded joints
Technical Information
Nozzle diameter | 19mm |
Number of nozzles/robot | 1 |
Blasting pressure | 7bar |
Abrasive | Steel grit |
Degrees of freedom | 8 |
Programming | Point-to-Point or Teach-in |
Operation mode | Automatic or manual |
SOLUTION
The blast room was robotized by one Blastman B20S robot equipped with a camera system and a control room for touch-up blasting. The blast room was equipped with robot rails. The old recycling and ventilation system was integrated for robot operations and a new Blastman double chamber blast pot for continuous operations was included in the scope. The old transport wagon was integrated into the system.
3D model of blasting chamber with B20S robot
RESULTS
The robotized blast room works perfectly both in automatic and manual operations. The manual touch-up blasting is easy due to excellent visibility from the control room located well above the floor level and a supporting camera system to check the cleaning result in detail from a short distance.
You might be interested in these articles
Company News Events
03. Mar 2025
Welcome to visit us at MECSPE, Bologna from March 5th to 7th.
Blog Posts Company News Events
16. Dec 2024
Season´s Greetings from Blastman Robotics Ltd
Company News Events
23. Aug 2024
BLASTMAN AT INNOTRANS 2024
Blog Posts Company News Events
22. Aug 2024
ABRASIVE BLASTING INVALUABLE FOR RAIL INDUSTRY
Company News Events
20. Jun 2024
BLAST CLEANING LARGE STEEL STRUCTURES FOR ENERGY INDUSTRY
Company News Events
20. Feb 2024
WE´RE EXHIBITING AT PAINTEXPO 2024
Blog Posts Company News Events
18. Dec 2023