Upgrades and customer support
UPGRADES AND CUSTOMER SUPPORT
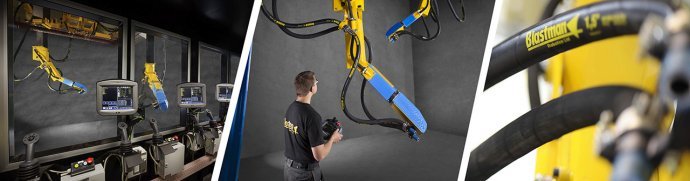
It has been four decades since Blastman Robotics designed and installed the first blast-cleaning robot. Generation 1 robots were designed one thing in mind, to be as durable as possible in harsh environments such as blast-cleaning chambers. Many years have passed after the first installation and since 2021 we have been providing state-of-the-art Generation 4 blast cleaning robots. Generation 1 and Generation 4 have 39 years between them, but one thing has not changed: our robots are still robust and designed to function and last many years in extremely harsh environments. Blastman robots are built to blast.
R&D has always played a significant role in Blastman’s strategy. Over the years, we have constantly been developing optional upgrades that extend our robot’s life cycle, reduce maintenance time, increase operator comfort, and overall make the blast cleaning process more efficient and user-friendly. Many of these upgrades have been seen as essential that they come as standard on our robots today. However, some upgrades are tailored for specific processes and are not necessary for all customers. The following upgrade options are a portion of our comprehensive and continuously growing supply.
Blastman Studio, offline programming software
Thanks to our continuous R&D efforts, we have launched our own software for programming Blastman robots. The software is included with all new generation 4 robots and can be used with previous-generation robots as well. Offline programming can be done outside production with zero process downtime. With Blastman Studio you get optimal process performance and greatly increased efficiency. The software has a visual user interface and is comparable to playing a video game. Most users of the software are ex-manual blasters. All programmers are trained by our specialists and support is always easily available.
Offline programming software Blastman Studio
Blasting robot programming hand panel
Automatic pressure adjustment in Blastman Studio
Some areas of the workpiece might require a tougher impact of abrasive or a more gentle touch. Blasting pressure can be adjusted automatically via Blastman Studio to clean specific areas with an appropriate pressure level. This is needed in case the material strength changes in the workpiece. In railcars and trailers, substrate thickness can be as low as 3 mm. This requires a lower pressure compared to other areas of the car to eliminate the risk of deformation. On the other hand, with castings, some areas may contain tougher burnt cast sand that requires a higher pressure than other areas. The process can be optimized with different pressure levels to reduce hose wear and save on operating costs. Blasting pressure can also be decreased for manual blasting purposes.
Machine vision
Machine vision brings out the best aspect of automized blasting process, letting the machine do the work for you. The system automatically recognizes different workpieces that arrive at the blasting chamber. The system processes the exact location and orientation of the workpiece; picks the correct blasting program and the robot continues to do what it's built to do – to blast, without the need for intervention from the operator.
Blast hose break monitoring
In high-pressure blasting, abrasive particles are travelling with high velocity inside blast hoses and cause more wear compared to manual blasting with lower pressure. Overall efficiency is much higher in robotic blasting and hoses wear more due to increased mass flow. A worn blast hose can break during blasting and the operator needs to monitor the process and be prepared to pause in case of hose rupture. Blast hose break monitoring automatically stops the ongoing program in case of hose rupture and eliminates the risk of the robot running automatically with a broken hose. The operator is informed in case of hose breakage and constant process monitoring is not needed. The system is also used to monitor the condition of our blast pot exhaust valves. In case a membrane is worn, the system detects this issue and notifies the operator.
Blast hoses and nozzles
MES Connection
Our robots can be connected to manufacturing execution systems. Real-time production planning and controlling play a key role in managing production as effectively and efficiently as possible. The production manager can predict workpiece and robot availability from the office using process information shared to his/her display and release real-time information to the next production lines for optimized output.
Customer support
Our goal is customer satisfaction and long-term relationships throughout the lifetime of our equipment, which can be well over 20 years when a proper preventive maintenance program has been followed. Our customer support assists with any kind of inquiries, whether it is mechanical, electrical, software related, or any other topic.
Robot arm maintenance
We will gladly provide you more information of our wide range of upgrade options, all inquiries and support requests can be sent to one address: aftersales@blastman.fi
Juuso Takkinen
Key Account Manager
Blastman Robotics Ltd
More interesting articles to read:
Aftersales services improve investment value and productivity
Blastman working closely with customer for achieving the best result
Visit also our BLASTMAN SERVICES page.
You might be interested in these articles
Blog Posts Company News Events
15. Aug 2025
ABRASIVE BLASTING INVALUABLE FOR RAIL INDUSTRY
Company News Events
03. Mar 2025
Welcome to visit us at MECSPE, Bologna from March 5th to 7th.
Blog Posts Company News Events
16. Dec 2024
Season´s Greetings from Blastman Robotics Ltd
Company News Events
23. Aug 2024
BLASTMAN AT INNOTRANS 2024
Company News Events
20. Jun 2024
BLAST CLEANING LARGE STEEL STRUCTURES FOR ENERGY INDUSTRY
Company News Events
20. Feb 2024
WE´RE EXHIBITING AT PAINTEXPO 2024
Blog Posts Company News Events
18. Dec 2023