ROBOTICS IN PRE-TREATMENT
ROBOTICS IN PRE-TREATMENT
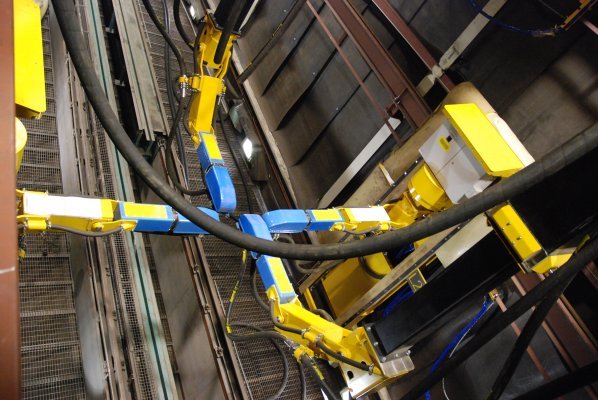
Robotics is increasingly finding its way into the surface pre-treatment of coatings by blasting. However, special robot technology is required for this abrasive application, as standard industrial robots are not able to do this.
In surface technology, metal components must have a defined cleanliness and reproducible surface quality before coating. Blasting technology is often used to achieve this. Cast parts are also primarily cleaned of adhesions by blasting before further mechanical processing. Manual blasting is very laborious and dangerous, as the workers are exposed to high physical stress, noise, and dust. This is particularly true when blast cleaning large components such as the bodies of rail vehicles or engine blocks of large ships. Fewer and fewer employees can be recruited for this strenuous activity.
Up to now, blast wheels and pressure blasting machines have been used primarily for automatic blast cleaning, but their application possibilities are limited. They are only suitable for processing simple components of a certain type and size. Multi-axis industrial robots are much more suitable but impractical due to the abrasive environment. Dust and
blasting particles damage the equipment and impair its function and service life. Although covers can improve protection here, they further restrict the working area of stationary industrial robots, meaning that the component often has to be rotated additionally. Robots specially developed for blasting on gantry bridges or wall rails, on the other hand, meet all requirements. In combination with a control cabin, they can also be used as manipulators for blasting individual or special components.
History and development: Hydraulic blasting robot after 26 years of use (left) and modern
blasting robot with servo-electric drives (right).
Development of blasting robots
The first robots specially developed for blast cleaning were manufactured in the early 1980s by the Finnish steel group Rautaruukki to facilitate the surface pretreatment of large steel components, such as bridge elements, before coating. The first external users of these blasting robots with significantly improved durability were companies such as ABB, Alstom and Siemens, who used these blasting robots, which were still hydraulic at the time, for the automatic blast cleaning of large transformers, passenger cars, and turbine housings.
In 1998, a management buy-out resulted in the current company Blastman Robotics, which develops special blasting robots for a wide range of applications and markets and sells them worldwide. Since then, there has been continuous development in this special field of robotics, which, in addition to hardware and software development, also includes control based on information processing. The aim is to create a controlled interaction between the electronics and mechanics of the respective blasting robots for various applications through the simplest possible programming and operation.
Programming is possible in the following ways:
- Online Motion Recording (OMR): Teach-in during beam processing with the manipulator,
- Point-to-Point (PTP): Point-to-point with the hand-held teach-pendant,
- Offline programming (OLP): 3D programming & simulation on a PC,
- Parametric Path Generation (PPG): For components with simple geometry.
When parametrically programming components with simple geometry, such as containers or pipes, the latest software eliminates the need to create a program line yourself. It is sufficient to simply enter the dimensions such as the diameter and length of a pipe and the software generates the corresponding blasting program for the robot itself.
Digitization of pre-treatment
Large metal components with complicated geometries require complex motion sequences for robot-based blasting processing. Special software tools such as
Blastman Studio enables intuitive programming on the PC without having to interrupt production. The CAD data of the components can be easily imported into the software’s 3D simulation environment. This is then used to create the individual motion paths for the respective blasting robots. From this summer, this will also be possible using inverse kinematics. The reverse transformation will then make it possible to determine the joint angles of the blasting robots’ arm elements based on the position and orientation of the end effector. The integrated simulation tool for the visual representation of the blasting process can also be used to identify potential collisions and optimize the blasting programs in advance.
By using the 3D data of the components to create the blasting programs and the generation of digital data by the robot to control and monitor the blasting process, digitalization is increasingly being used in surface pretreatment. Together with digital control and monitoring of air and abrasive reprocessing in the blasting chamber, the exchange of data for quality assurance and operational production management for production planning and control is also supported. Blasting robotics in combination with a smart blastroom thus enables the big data connection of surface pretreatment in accordance with Industry 4.0.
Robot blasting chamber for freight wagons.
Durable and reliable
The most important reason for replacing manual blasting with robotics, apart from the strain on employees, is productivity. Modern blasting robots made of wear-resistant materials, equipped with powerful drives and the latest software can achieve blasting performance up to 15 times that of a manual blasting worker. Depending on customer requirements and the number, shape, and size of the components to be cleaned, solutions ranging from simple stationary blasting robots to 8-axis gantry robots are used. Multi-axis blasting robots, which can reach all areas of even large blasting chambers, also have the advantage that they can always process the components with the optimum blasting distance and blasting angle. This gives the component a uniform blasting pattern with the degree of preparation required for the subsequent coating with reliable repeatability
everywhere.
In addition, the level of programming and expertise in the use of robotics has developed rapidly in recent years, further improving the already high reliability and service life of the blasting robots. As a result, the overall efficiency of the blasting process has increased enormously, meaning that surface pre-treatment can not only be carried out faster and more safely, but also more cost-effectively and with higher quality.
Author
Heiko Reski
Sales Manager
Blastman Robotics Ltd, Düsseldorf (Germany)
You might be interested in these articles
Blog Posts Company News Events
15. Aug 2025
ABRASIVE BLASTING INVALUABLE FOR RAIL INDUSTRY
Blog Posts Company News
03. Jul 2025
BLAST CLEANING SOLUTIONS FROM KEMPELE* TO BRAZIL
Blog Posts Company News
17. Jun 2025
WHICH ROBOTIC BLAST CLEANING SYSTEM IS RIGHT FOR YOU?
Blog Posts Company News
31. May 2025
BLAST CLEANING METALWORKING MACHINERY
Blog Posts Company News
13. May 2025
BUILT TO BLAST - HOW TO MAKE ROBOTS LAST FOR DECADES
Company News
03. Apr 2025
BLASTMAN BLAST CLEANING ROBOTS IN DIFFERENT INDUSTRIES
Blog Posts Company News
01. Apr 2025