BLASTMAN BLAST CLEANING ROBOTS IN DIFFERENT INDUSTRIES
BLASTMAN BLAST CLEANING ROBOTS IN DIFFERENT INDUSTRIES
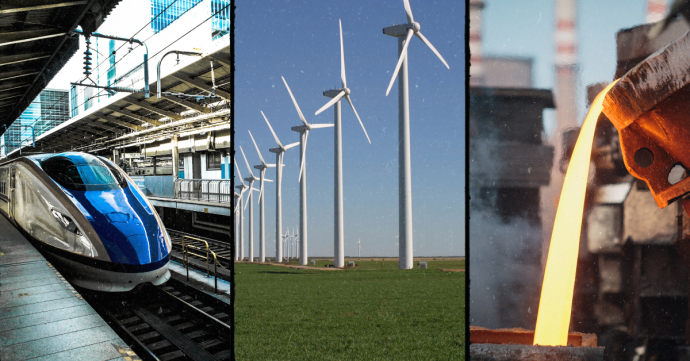
BLAST-CLEANING RAILWAY CARS
PROCESS
The plant consists of two 8-axle portal-type Blastman B20C robots, which are installed in the blast room and equipped with a moving control cabin. The booms of the robot are designed so that the blast jet is able to reach all cleaned areas, both inside and outside the cars. The use of heavily dusting blast media has been taken into account in the design of the robot.
SOLUTION
The robots clean the workpiece with mineral shot grit blasted through a 16 mm venturi nozzle at 6.5 bar pressure. The workpieces are passenger and freight cars with aluminum and steel structures. The cleaning of serial production cars is fully automated. Single cars can be cleaned by operating the robots as manipulators.
OBJECTIVES
Blast cleaning had become a production bottleneck. Wall-mounted manipulators that have been in use since 1988 should be replaced with automatic equipment capable of flexible production. Manual touch-up was to be minimized to increase worker safety and effectiveness. The outcome of the cleaning should meet the other requirements of surface treatment as well as possible.
Technical information
Nozzle diameter | 16mm |
Amount of nozzles/robot | 1 |
Blast pressure | 6,5 bar |
Blasting rate | 100-150 m2/h/nozzle |
Cleanliness | Sa 2,5/Sa 3 |
Abrasive | mineral - garnet |
Degrees of freedom of the booms | 8 |
Degrees of freedom of the control cabin | 2 |
ADVANTAGES OF THE ROBOT
- considerable savings in production costs
- increased production capacity
- remarkable health and safety implications
- freedom to use any abrasive material
- desired surface cleanliness and roughness
- slight surface shaping by controlling the blast pressure
- working lifts and platforms are unnecessary
- increased fatigue strength of specific welded joints
RESULTS
The plant cleans serial production cars fully automatically. The production can be handled according to goals, there are no bottlenecks. The robots clean the cars unattended, enabling the person to perform other tasks.
CUSTOMER EXPERIENCE
“We are already operating with the third-generation Blastman robots. Maintenance costs are low, even though we use robots in three shifts.”
Business owner
See more of our railway references
WIND TURBINE TOWERS
BACKGROUND
Previously, the customer had blast cleaned the external surface of the wind turbine tower manually. To gain more productivity and standard quality, customers contacted Blastman Robotics to solve this problem. It was determined early on that the Blastman B12S blast cleaning robot would be a suitable robot model to solve a customer's needs. The B12S G4 robot is the optimal solution for blast cleaning the wind turbine tower's external surface. With this simple and cost-effective robot model, the ROI of the customer is ensured to be feasible.
Blastman B12S robot blasting wind towers
OBJECTIVES
The goal was to offer customers a fully automated blast cleaning process for the external surface of the wind turbine tower. Blastman robotic solutions provide productivity, efficiency, and standard quality for the customer, as well as improved safety and working conditions.
The B12S G4 robot is the optimal solution for blast cleaning the wind turbine tower's external surface. This simple and cost-effective robot model ensures the customer's ROI is feasible.
Technical information
Nozzle diameter | 19 mm |
Amount of nozzles | 2 |
Blasting pressure | 8-10 bar |
Blasting rate | 150-200 m2/h |
Cleanliness | Sa 2,5 |
Abrasive | Steel grit |
Degrees of freedom | 4 axis |
Programming | Parametric programming |
Operation mode | Automatic |
SOLUTION
The customer's blast room is equipped with a Blastman B12S robot. The robot uses two 19mm nozzles with 8-10 bars of pressure. Before starting the blast cleaning process, operators input the tower data into the parametric programming software in the user interface outside the blast room. The software automatically creates and saves the program, and the robot will adjust its position and movement according to the tower diameter. The Blastman B12S robot, combined with the parametric programming software, provides an extremely simple and extremely productive blast cleaning process for the customer.
RESULTS
Through process optimization, the capacity requirements have been met. Customers can blast clean up to 200 m2/h to Sa 2,5 cleanliness. The safety and working conditions of the operators have increased drastically. This is a true testament to what can be achieved by incorporating the latest technology in the blast cleaning process.
CUSTOMER EXPERIENCE
“The Blastman robotic blasting machine produces a continuous, uniform and high quality blast. Blastman products have a robust design that can withstand the extreme requirements of blasting.”
Rudolf Seefeldt, Enercon, Germany
See more of our wind power references
LARGE CASTINGS
BACKGROUND
Blasting is the most widely used method for cleaning and surface treating cast parts. Blast cleaning involves completely removing sand and cores from the components and also reliably cleaning and compressing the cast surfaces to achieve a specified level of cleanliness and surface quality. Manual blasting is a demanding process that presents hazards for the workers, who are exposed to a high level of physical stress as well as noise and dust.
Blastman B20S blasting large castings
OBJECTIVES
The requirement was to blast clean various large cast parts, such as crankcase, and both automatically and in manipulator mode.
Technical information
Nozzle diameter | 19mm |
Amount of nozzles | 2 per robot |
Blasting pressure | 10 bar |
Blasting rate | up to 200 m2/h |
Cleanliness | Sa 2,5 |
Abrasive | Mix of steel grit and shot |
Degrees of freedom | 8 axis |
Programming | Teach-In, PTP, Offline |
Operation mode | Automatic, manipulator |
SOLUTION
The multi-axle Blastman B20CX robots are mounted on gantries and can reach every corner of the blasting chamber. In combination with a control cabin, they can also be used as manipulators to blast individual or special workpieces. By contrast, when processing mass-produced components, the blasting robots repeat shared programs. They automatically follow the contours of the component and aim directly at areas that are difficult to access.
The result is a high and reproducible standard of quality with no human input or errors and without the excessive levels of blasting produced by blast wheels. In addition, the robots can operate at a blasting pressure of up to 10 bar, which allows for high abrasive speeds of up to 200 m/s.
The robots are programmed using a teach-in or point-to-point process with a handheld touch-screen control panel. Only basic familiarization is needed. Offline programming is a particularly efficient process because the 3D component data is taken directly from the design engineering department. The simulation shows all the movements of the robot on the screen in the form of a 3D model. The movements can be fine-tuned offline to improve the quality and reduce the time needed for the process.
RESULTS
Outsize cast components weighing up to 200 tonnes can be blasted by a robot in the new blasting chamber using a fully automated process. As a result, the work can be carried out not only more quickly and safely, but also at a lower cost and to a higher standard of quality.
In addition, the robots remove abrasive residues and dust from the components quickly and effectively using compressed air after the blasting process. This means that the parts can move on to the next production phase more quickly and the blasting chamber is available for reuse much sooner.
CUSTOMER EXPERIENCE
“Our Blastman equipment is for blast cleaning, which is what the company stands for in cast parts: fast, reliable, highly efficient, and top-quality results. By using special blasting robots, such work is not only carried out more quickly and safely but also cheaper and with higher quality.”
Business owner
See more of our foundry references
You might be interested in these articles
Blog Posts Company News Events
15. Aug 2025
ABRASIVE BLASTING INVALUABLE FOR RAIL INDUSTRY
Blog Posts Company News
03. Jul 2025
BLAST CLEANING SOLUTIONS FROM KEMPELE* TO BRAZIL
Blog Posts Company News
17. Jun 2025
WHICH ROBOTIC BLAST CLEANING SYSTEM IS RIGHT FOR YOU?
Blog Posts Company News
31. May 2025
BLAST CLEANING METALWORKING MACHINERY
Blog Posts Company News
13. May 2025
BUILT TO BLAST - HOW TO MAKE ROBOTS LAST FOR DECADES
Company News
03. Apr 2025
BLASTMAN BLAST CLEANING ROBOTS IN DIFFERENT INDUSTRIES
Blog Posts Company News
01. Apr 2025