BLAST CLEANING OF EXTERIOR SURFACE OF WIND TURBINE TOWERS
BLAST CLEANING OF EXTERIOR SURFACE OF WIND TURBINE TOWERS
Case: WINDAR RENOVABLES Aviles Asturias, Spain
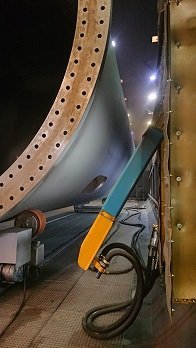
Over the years, Windar Renovables has accumulated extensive know-how, which has allowed them to position itself as one of the world’s leading manufacturers of wind turbine towers and one of the most active players in the fabrication of offshore foundations.
BACKGROUND
WINDAR Renovables has always been at the forefront of innovation when talking about using the latest technology to optimize production processes. Cooperation between Blastman Robotics and Windar began in the year 2019 when Blastman was tasked to provide an automatic solution for wind turbine tower exterior surface blast cleaning to replace manual blast cleaning.
Blastman Robotics delivered a robotic solution that significantly increased the productivity and efficiency of the blast cleaning process compared to manual blast cleaning.
OBJECTIVES
The objective was to automatically blast clean the complete exterior surface of the wind turbine tower to the cleanliness level of SA 2,5 and SA 3,0 in a given cycle time. Also to provide standard high quality and reliability to the blast cleaning process.
As a result of automating the blast cleaning process, overall safety of personnel is also improved by minimizing the need for manual blast cleaning.
TECHNICAL INFORMATION
Nozzle diameter | 16mm |
Number of nozzles/robot | 2 |
Blasting pressure | 8 bar |
Blasting rate |
160 m2/h exterior surface |
Abrasive | Steel grit |
Degrees of freedom | 5 |
Programming | Parametric programming |
Operation mode | Automatic |
SOLUTION
Blastman B12S G4 robot was installed into the existing blast room as a retrofit project. To ensure a continuous flow of abrasive to feed to the robotic solution, Blastman blast pot 1400 was also installed. This solution can provide non-stop operation to the customer for the blast cleaning of the exterior surface of wind turbine towers.
Products are transported and rolled in roller beds. Blastman encoder was installed into the roller beds to ensure automatic rotation of the tower and enable communication with a robotic solution. Blasting is done from sector to sector in the longitudinal direction with two 16mm nozzles on the robot. Overlap between nozzles ensures the stripe is blast cleaned efficiently and leaves cleanliness levels of SA 2,5 and SA 3,0 as surface results.
Blasting chamber for wind tower exterior blasting
RESULTS
With Blastman B12S G4 robotic solution and parametric programming, software customer is able to achieve the required cleanliness level more efficiently than normal manual blasting operation. Also, reliability and standard high quality are achieved throughout the blast cleaning process.
Because of the globally increasing demand for on-shore and off-shore wind turbine towers, the customer is able to meet high production outputs by implementing automatic blast cleaning operations.
3D model of blasting chamber for wind tower exterior blasting
“With the Blastman B12S robot our productivity has improved, and it also enables optimizing our production planning. Now we know in advance the exact time which will be spent for exterior blasting on each piece. Furthermore, personnel can carry out other activities while the robot is working.”
-Iván Álvarez, Process Engineering Leader, Windar Renovables
You might be interested in these articles
Blog Posts Company News Events
15. Aug 2025
ABRASIVE BLASTING INVALUABLE FOR RAIL INDUSTRY
Blog Posts Company News
03. Jul 2025
BLAST CLEANING SOLUTIONS FROM KEMPELE* TO BRAZIL
Blog Posts Company News
17. Jun 2025
WHICH ROBOTIC BLAST CLEANING SYSTEM IS RIGHT FOR YOU?
Blog Posts Company News
31. May 2025
BLAST CLEANING METALWORKING MACHINERY
Blog Posts Company News
13. May 2025
BUILT TO BLAST - HOW TO MAKE ROBOTS LAST FOR DECADES
Company News
03. Apr 2025
BLASTMAN BLAST CLEANING ROBOTS IN DIFFERENT INDUSTRIES
Blog Posts Company News
01. Apr 2025